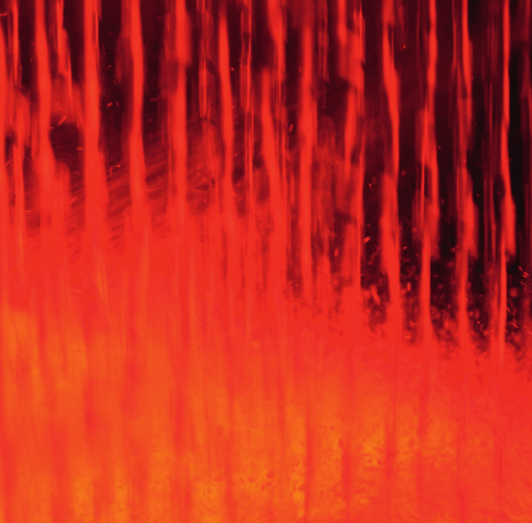
Increased steel production with optimized cooling
Through the advanced control of a number of cooling ramps at SSAB’s strip steel plant in Borlänge, Optimation was able to help the steelmill to increase capacity. At the same time, large amounts of electricity were saved.
Steelmaking is an energy-intensive operation. You have to both heat and cool, both of which draw large amounts of electricity. It is all about optimizing all parts of the process and, for Optimation, it was about making sure that the showers that cool the strip steel would not use more water than necessary. Pumps are powered by electricity, and previously they used excessive amounts of energy at SSAB. The requirement for the project was to reach a margin of five percent with a short turnaround time.
“The challenge for us at Optimation was to create a control system that could quickly get the right flow in the showers,” says Johan Simonsson, project manager at Optimation. “Today, the amount of cooling water applied to the strip is calculated by the parent control system. With this control we have been able to reduce the circulation of water, thereby reducing energy use.”
A complicated project
Johan Simonsson admits that it was first thought that the assignment would be relatively straightforward, given the experience gained by Optimation after a number of years with many projects in the process industry.
“We set up a simulator and looked theoretically at the task. After a while, we realized that the project was far more complicated than we had imagined before we started. There were long and deep discussions both at Optimation and with SSAB.”
SSAB had addressed the problem on its own before deciding to hire a third-party consultant with control system expertise. They therefore had much to contribute with regard to proposals and the requirements posed by the process.
SSAB increased the production rate and cut energy use by 60%
“SSAB manufactures steel with different recipes, which vary in the material used in the strip plant and which may require different handling. This means that it must be possible to change systems quickly. When the new shower system was in place, SSAB could therefore increase the rate of production by shortening the distance between different steel semis sent through the strip plant.”
The process control that Optimation brought forward is of the physical feedforward type. This type of control is fast, but it requires an accurate and reliable model to provide the desired function. In SSAB’s project it was important that the control was fast, and the Optimation model proved to work well in terms of speed and optimization of water flow. Since the new controls have been introduced into operation, energy use has been reduced by about 60 percent, while the steel producer also has increased production capacity.
“SSAB is very pleased with the results of the project, which was very rewarding for project participants on both sides,” says Johan Simonsson. “SSAB had a lot to add in the discussions and they really brought the project forward. At the same time, Optimation and the simulator we have built up and used throughout the project enabled us to try out different strategies to see what effect they could have.”