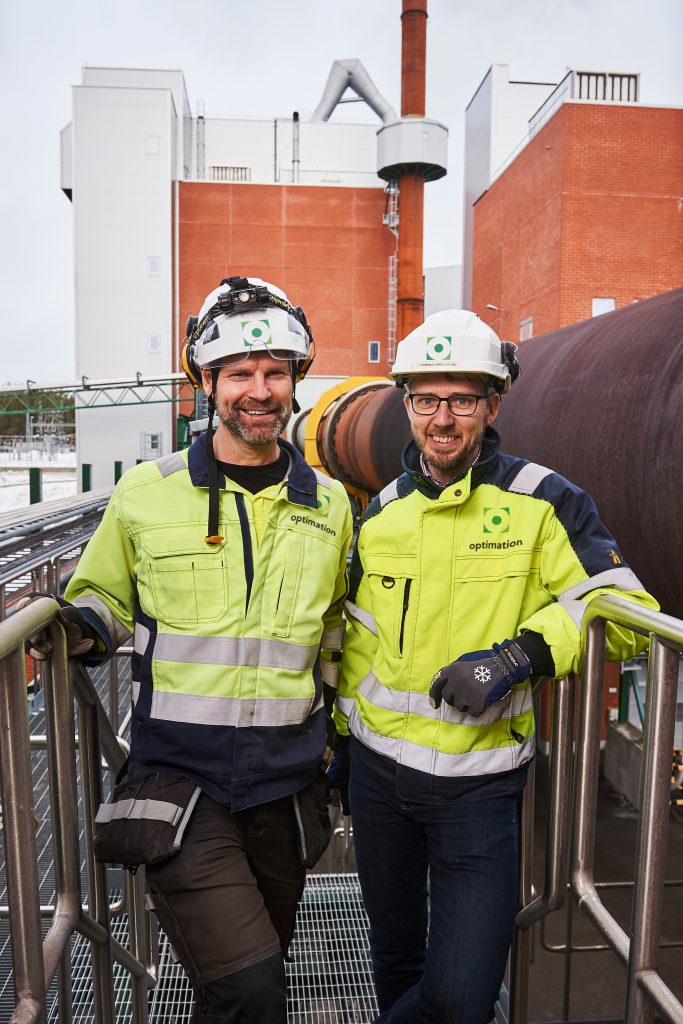
New patented solution to an 80-year-old problem
Optimation has recently been granted a patent for its solution to an 80-year-old problem. Good process control can help to reduce fuel consumption in lime kilns in the pulp and paper industry. The technology can also be applied in the lime and cement industry, which is second only to the steel industry when it comes to carbon dioxide emissions in Sweden.
Since they began to be widely used in the pulp and paper industry in the1940s, it has been a known fact that it is important to maintain stable temperatures in lime kilns. Several solutions to the problem have been implemented, but none have been widely adopted.
“We’ve had the idea for this patent for a long time, but we haven’t had a customer who was prepared to invest in a whole new way of thinking,” explains Erik Berg.
When SCA Munksund built a new kiln they also decided to introduce a new master control system and they chose Optimation’s solution.
“I had previously heard that control systems for lime kilns hadn’t been very successful, but what made me believe in Optimation’s solution was their reasoning as to how various parameters affect the process and that there was a simplicity to it that made it very easy to understand. Looking back, we are very satisfied with the result and I also think that the consistency that is enabled by the control system also prevents the build-up of rings and balls, which can be a big problem in lime kilns,” says Fredrik Lind (operations specialist at SCA Munksund).
Optimation has for some time been looking at various multivariable controllers for lime kilns. However, these technologies are rather advanced and it is not always easy for personnel at the mills to learn how they work, so we came up with something simpler and more robust. The challenge is that the two temperatures that can be measured in a rotary kiln are not independent of each other; therefore, two independent controllers cannot be used to control them. The solution we came up with is both simple and ingenious and is based on what is referred to in control engineering as decoupling. In simple terms, average temperature and temperature difference in the kiln are calculated, and these two temperatures, unlike the measured temperatures, are independent of each other and can therefore be controlled via PID controllers, the most common type of controller used in the industry.