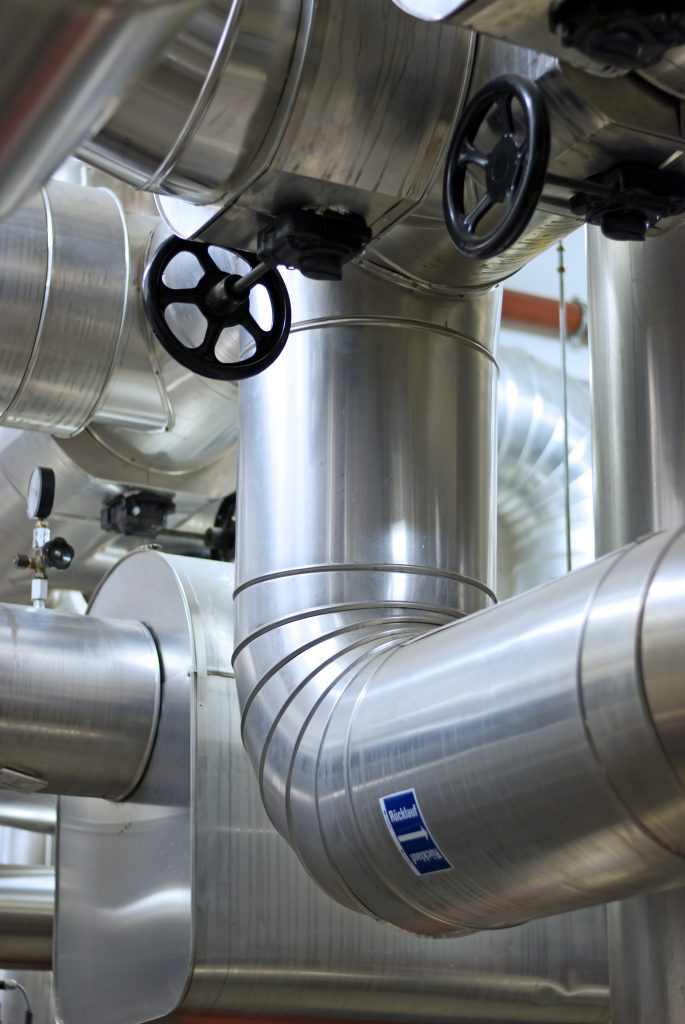
Control is the core of Billerud Korsnäs’s steam system
When Billerud Korsnäs in Gävle was to rebuild and upgrade its energy production facility, the development of new control strategies began early in collaboration with Optimation AB.
Getting involved from the start is a dream for all control system engineers, a profession that is often consulted too late in major industrial projects.
“Billerud Korsnäs’s strategy was to entrust Optimation to manage the control system of the existing steam grid from the beginning,” says Andreas Krafft.
To succeed in implementing a simple and well-conceived control strategy, being part of the project from the outset is a huge advantage. With this approach, the challenge is that you can work on repeated installations over a long period of time as new installations are realized.
Andreas Krafft appreciates the opportunity to participate throughout the project with new steam systems at Korsnäs.
“Optimation’s project model lets the control needs of the components determine how a plant and control system should be built.”
By applying this approach to Korsnäs, Optimation has fully implemented its principle of having a control device for each pressure level that must be controlled, and having a clear priority order in the system.
It has long been common in industry to have one controller per valve, and it often leads to them ‘fighting’ each other,” says Andreas Krafft.
Many possibilities to control
The steam system at the Gävle plant, operated by the newly formed company Bomhus Energi AB, consists of a number of different pressure levels. A new boiler and a new turbine are also part of the project. The aim is to send as much steam as possible through the turbine. To increase efficiency further, utilization of the large steam accumulator, with 300 cubic metres of water, is increased. The accumulator allows the system to maintain the pressure in the network during temporary disturbances in steam usage. The system also manages to change the load in the boiler slowly, giving the boiler an opportunity to reset without disturbing operation.
Alternatives such as dump condensers and free-blowing should only be used as a last resort in the control strategy. Of course, the system is automatic and designed to cope with all the different operating scenarios. Much effort has also been made to provide an overview of how the system is working.
As is often the case in major industrial projects, an important factor is that old equipment still remains well into the project. In this project, for example, the old turbine and boiler will still be in operation, even after the new control system is fully connected.
Three years with Billerud Korsnäs
The project at the Gävle plant has been under way since spring 2010. At that time, a prestudy was made based on the current needs.
“A good preproject is important,” says Andreas Krafft. “This allows you to build a good simulator and thus create a good base for the continuation of the project.”
The main project began in autumn 2010.
“Then, we built the simulator. Together with a group of people with different skills, we looked at different operating scenarios. We then modified the simulator according to the needs we could identify.”
When everyone was satisfied with the simulator, the programming was done by a subcontractor.
In March 2011 it was time for the first commissioning. Since then, Optimation has had intense working periods as various parts of the plant have been put into operation. The last parts of the control system came into operation in December 2012.
“Towards the end of the project, more and more suppliers have come in, including ÅF, Siemens and Metso. Together, we have had many discussions about control strategies and technical solutions.
Although the work has been complicated, we have kept to the timetable from start to finish. This has been a very successful project,” concludes Andreas Krafft.