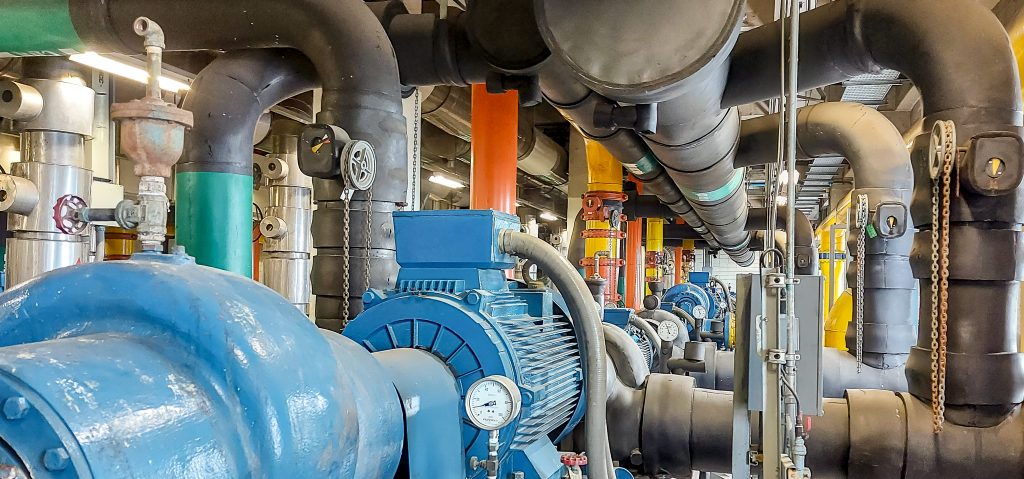
New control and pump for feed water in Hylte
The Hylte paper mill wanted feed-water pumping to work automatically. Operators would thus be free to work on other issues that required more attention.
Optimation created a new control system that, together with a new pump, gave the mill an efficient and fully automatic control of the feed water facility.
“Hylte wanted a control system that required as little interference as possible,” says Björn Söderlund, Optimation. “Ideally, none at all. The operators would be able to rely on the automation and focus on more important things. At the same time, Hylte wanted a feed water system that used as little energy as possible, which was achieved by optimizing the pressure level to provide the required pressure, but no more.”
Since one pump uses less power than two, one of the proposed measures was to replace one of the five pumps with a 50-percent-larger one, which was also speed-regulated.
The larger pump was dimensioned to meet the entire need on its own, when that was at a normal level. Previously, the pumps’ size meant that the capacity requirement was somewhere between one and two pumps, necessitating many starts and stops of the pumps. In combination with the fact that two of the pumps lacked speed-regulation, it all led to unnecessarily high energy consumption.
Control with as little intervention as possible.
We created fully automated control
Optimation had created the control system that existed before the latest project as well, and that system had worked very well. But changes in production at Hylte also changed the requirements of the plant’s feed water system, and regulation of the pumps hence became less efficient. Therefore, a new project was carried out to install the new larger pump, and Optimation was engaged to adapt the control system for this pump. “But the project became larger, and we created a fully automatic control system,” says Björn Söderlund. Optimation noted during the project that control would be more effective if, instead of speed control, the pumps could be regulated with respect to torque, which is proportional to both power and flow.
“It is quite unusual to run different-sized pumps in parallel, as we do at Hylte. If we had used speed regulation only, it would probably have meant that the largest pump would often have had to do all the work, instead of optimizing pump operation from an energy point of view,” says Björn Söderlund.
Joakim Wallbing at Optimation worked a lot on the project and he was the one who developed the simulator for the new automatic control.
“Since we were able to control the torque of each pump separately, it was like opening one valve at a time,” says Joakim Wallbing. “The control system is now in normal operation, works automatically and provides energy-efficient pumping of feed water.”